Blog and News
Tips for Installing Epoxy Flooring in Cold Weather
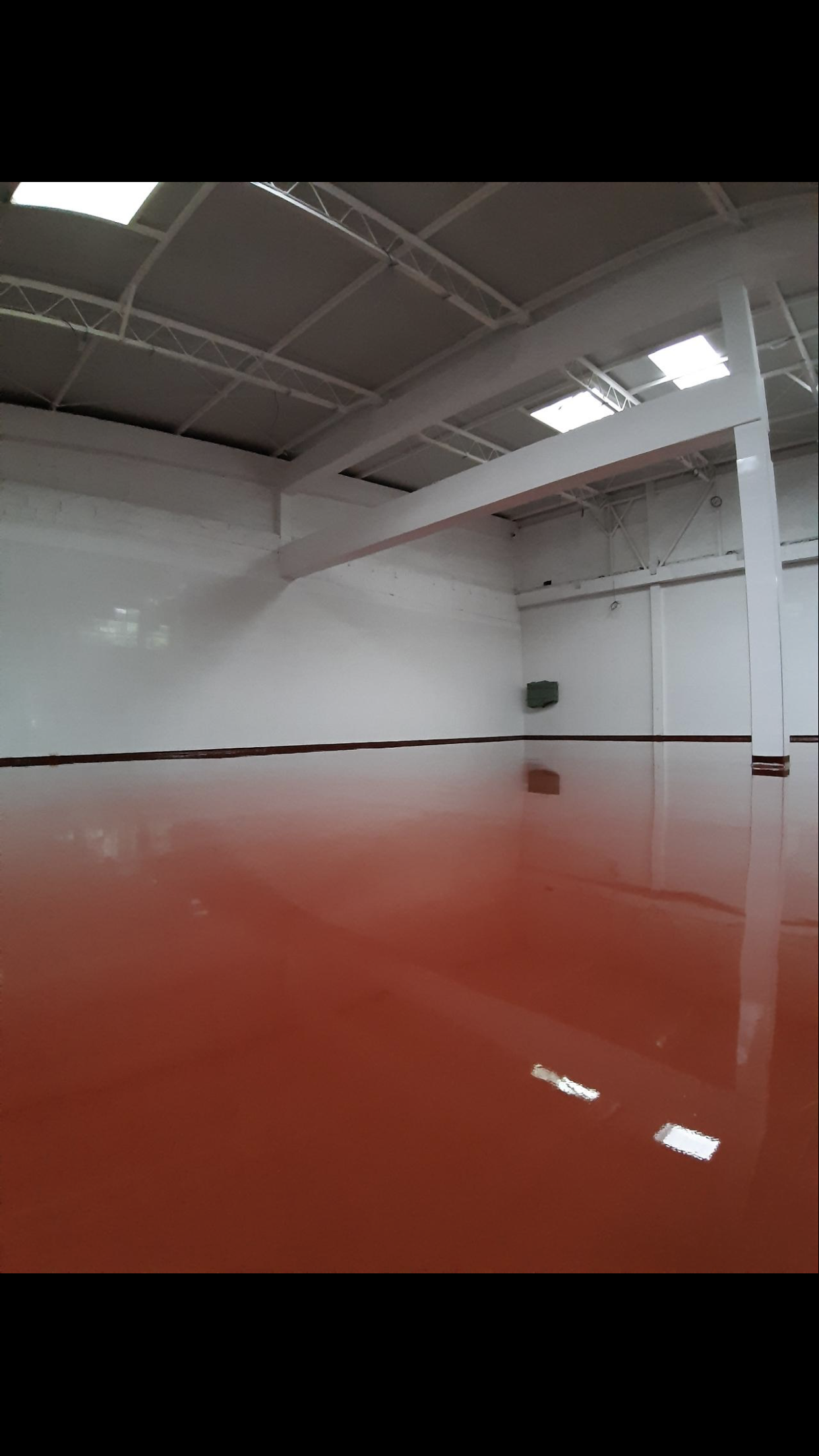
Now that cooler months are upon us, you will need to cogitate how the cold weather will impact application possessions and curative, and how you should store materials in this environment. Don’t forget to take the following into account:
How Low Can You Go?
To start, you need to determine the lowest temperature you can put on the material and just how long can it take to heal. For most standard epoxies, that is 60 degrees F. For fast treatment or low-temperature treatment epoxies, its 45 degrees F.
There is some Epoxy Coating which can heal down to 20 levels. While they can heal well at low temperatures, they only have chemical resistance, so they’re not appropriate for all applications.
Understanding Environmental Conditions
Once you have determined the lowest temperatures, you need to assess your environmental conditions. For example, what’s the ambient air temperature and relative humidity? What’s the slab fever? Slab temperature is important because if the atmosphere is 65 degrees and the slab is 45 degrees, a coat that is designed to heal down to 60 levels simply won’t fix to a suitable degree. It is going to cure partially, leading to chemical resistance and reduced physical properties. Occasionally this doesn’t pose an issue, but failure can lead to more demanding applications.
Be Aware of Installation Challenges
With regards to installation, chilly weather could make everything more strenuous since the working properties of the epoxy coatings change radically. That coating that CPS may become 2000-2500 CPS. This implies it’ll be more difficult to squeegee, trowel or roster. Also, the coating will not flow and level as well. While normally not an issue for coatings over 10 mils, at 6-8 mils you will see some orange peel which you wouldn’t see during the installation of a temperature.
Installations from the cold – and – particularly cold and humid conditions – are more susceptible to amine blushing. This manifests as an oily film on the coat, along with a reduction of gloss. If not addressed, the amine blush will cause jacket adhesion failure. If blushing occurs, the floor ought to be cleaned with a water and vinegar solution, and then followed with a thorough mechanical abrasion before proceeding. That said, most epoxy coatings are resistant. While this occurrence is not likely, it is not impossible. It is better to bear in the rear of your mind.
Storing and Acclimating Materials
It is extremely important to store your material in 65-80 degrees F, if possible. Additionally, you wish to give your material time to acclimate at least twenty four hours, but 48 hours. Further, it is essential to be in search of crystallization from the resin side of the coat. Crystals are caused by thermal biking from hot to cold and may be reversed by heating the resin to 150 degrees F. Crystallized epoxy resins shouldn’t be used. Formulated or asbestos coatings have additives in them to prevent this from happening, but it can still happen.
Each season brings its own unique set of challenges. Careful education and planning might help ensure your success year-round.
Explore More Information: – Polished Concrete Floor Tampa